Spis treści
Oczywiście S-70i Black Hawk to nadal flagowy produkt spółki, ponieważ w PZL Mielec jest realizowany jego montaż końcowy. Stąd wylatuje gotowy śmigłowiec, tak jak z nowej linii produkcyjnej koncernu Lockheed Martin w amerykańskim Greenville wystartował 24 stycznia bieżącego roku pierwszy F-16 Block 70. Jest to najnowsze wcielenie tej maszyny, wyposażone m.in. w najnowszej generacji radar AESA i wiele innych rozwiązań zastosowanych w samolocie F-35 lub mających ułatwić współdziałanie z samolotami 5. generacji i kolejnych.
Najnowszy F-16 jest bliżej 5. generacji niż swoich korzeni
Coraz częściej można usłyszeć, że F-16 jest przestarzały, że to samolot z lat siedemdziesiątych ubiegłego wieku. Jednak w odróżnieniu np. od myśliwców MiG-29, które służą nadal w polski lotnictwie, F-16 były stale modernizowane i rozwijane. Najbardziej zmieniało się to, czego laik za bardzo nie zauważy. Może spostrzeże, że gdzieś przybyło anten czy innych „wypustek”, że owiewka przed statecznikiem pionowym staje się coraz większa, albo przybyło zasobników i dziwnych „garbów” które „przykleiły się” do kadłuba. Ale dla niego F-16, to F-16.
Ekspert wie natomiast, że w przypadku samolotów bojowych najważniejszy jest „wkład”. Fizyka, aerodynamika, nie zmienia się i działa na podstawie tych samych zasad. Przez ostatnie 70 lat nie wymyślono też lepszego napędu niż silnik odrzutowy. Staje się on nieco mniejszy, dużo bardziej wytrzymały, rośnie jego moc, ale to nie wpływa na możliwości samolotu tak jak elektroniczny „wkład” do samolotu bojowego. To postęp technologii w elektronice, łączności, radiolokacji i miniaturyzacji spowodował, że relatywnie mała, zwrotna i nieszczególnie droga, jak na swoją klasę, maszyna, może realizować zadania, które 30-40 lat temu wykonywały osobne klasy samolotów: bombowców, szturmowców, myśliwców, niszczycieli wrogiej obrony przeciwlotniczej, maszyn rozpoznawczych czy strategicznych.
F-16 Block 70 to samolot, który w „skorupie” samolotu generacji 4+ ukrywa wiele możliwości samolotu generacji 5. Nie korzysta z technologii stealth, ale potrafi komunikować się sieciocentrycznie, wykorzystywać informacje z innych źródeł. Nie tylko samolotów, ale też bezzałogowców, stacji naziemnych itp. Posiada rozbudowane sensory pasywne i systemy walki elektronicznej, środki ochrony przed wrogimi pociskamim ale też najnowsze generacje rakiet powietrze-powietrze, zdolne samodzielnie naprowadzać się na cele odległe o dziesiątki kilometrów.
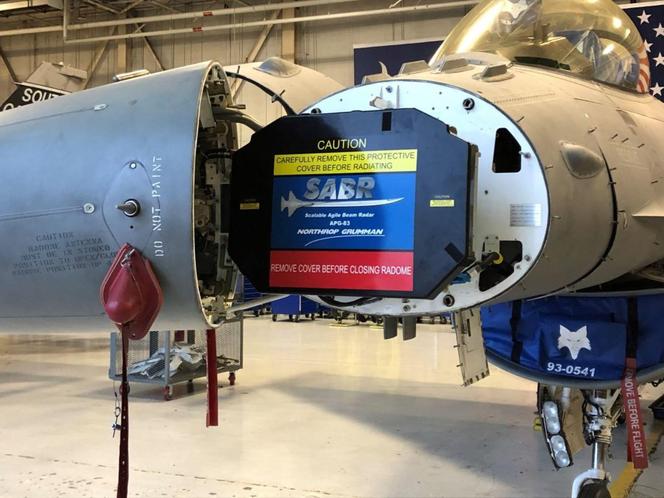
i
Rozszerzony pakiet uzbrojenia korzysta m.in. z większych zdolności wykrywania celów powietrznych i powierzchniowych oraz podniesionej odporności na zakłócenia stacji radiolokacyjnej APG-83 SABR (Scalable Agile Beam Radar), czyli rozwiązanie bazujące na postępach uzyskanych w ramach prac nad radarami AESA APG-77 dla F-22 Raptor i APG-81 dla F-35 Lightning II. W nazwie pojawia się określenie „skalowalny”, bo większa wersja tego radaru stosowana jest na bombowcach strategicznych B-1B Lancer. APG-83 powstał z myślą o zabudowie na starszych samolotach bez jakichś istotnych zmian w ich strukturze. Korzysta on z technologii AESA, czyli aktywnego skanowania elektronicznego. To znaczy, że antena zbudowana jest z wielu modułów nadawczo-odbiorczych, które mogą działać niezależnie i sterować wiązką fal radiowych bez obracania anteny. To znaczy, że np. część anteny może obserwować ziemię i wykrywać cele do ataku podczas gdy reszta mocy radaru skierowana jest na wykrywanie wrogich maszyn na niebie.
Cały ten zalew informacji przetwarza magistralę danych o wysokiej przepustowości oraz nowy komputer misji, a pilot otrzymuje informacje na centralnym wyświetlaczu wielofunkcyjnym (Center Pedestal Display), który zastąpił mniejsze ekrany i przełączniki. Uzbrojenie samolotu jest bardzo zbliżone do arsenału, jakim dysponuje F-35 i obejmuje najnowsze wersji rakiet powietrze-powietrze, pociski powietrze-ziemia dalekiego zasięgu, w tym pociski manewrujące JASSM-ER, oraz szeroką gamę bomb kierowanych, szybujących itp.
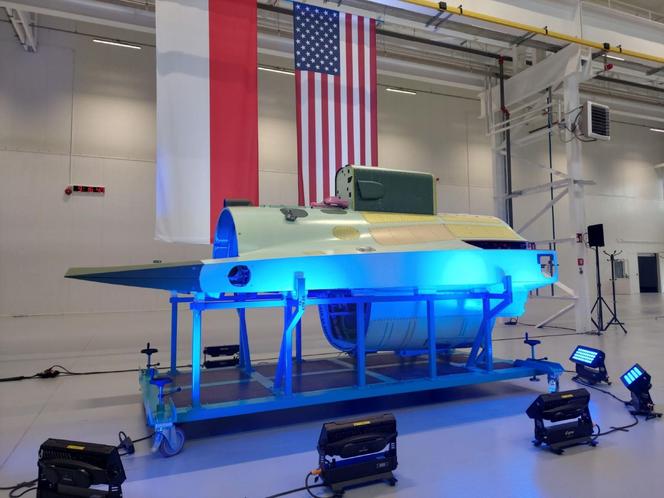
i
Nic dziwnego, że pomimo przerwy w produkcji, którą spowodowało przeniesienie linii do Greenville, dotąd zamówiono 148 samolotów F-16C/D Fighting Falcon Block 70/72 dla krajów takich jak Tajwan, Bahrajn, ale też Słowacja czy Bułgaria.
Rola Polski, czyli F-16 z Mielca
Może nie dosłownie cały F-16 z Mielca, ale faktycznie w należących do koncernu Lockheed Martin PZL Mielec powstaje dziś 50% struktury płatowca, czyli jego „ciała i kości”. Docelowo ma to być praktycznie cały kadłub, bez stateczników, skrzydeł i kilku drobniejszych element. Będzie to około 80% całej struktury płatowca i to całkiem niedługo.
Do USA trafiły już produkowane tutaj elementy struktury F-16. Najpierw przedniej cześć kadłuba, a dokładnie części otaczające kabinę pilota i przednią część, z wyłączeniem samego „dziobu”, czyli część osłaniającej antenę radaru. W Marcu tego roku wysłano do Greenville pierwsze elementy środkowej cześć kadłuba, do których mocowane są skrzydła i podwozie główne samolotu.
29 sierpnia niewielką uroczystością zakończono w Mielcu kolejny etap, którym jest wyprodukowanie pierwszego segmentu tylnej części kadłuba. Jest to obszar, w którym znajduje się silnik i mocowane są stateczniki poziome oraz pionowy wraz z długą „płetwą” czy też garbem kryjącym dodatkowe systemy elektroniczne. W elemencie zbudowanym w Polsce zintegrowane są też hamulce aerodynamiczne. Ten niepozorny element, który można zobaczyć na zdjęciach, podobnie jak wcześniej opisane, poleci niebawem do USA, aby przejść końcowe testy i stać się częścią nowoczesnego myśliwca.
W pewnym sensie jest to zwieńczenie pewnej drogi. Już obecnie w hali, w której odbyła się uroczystość, trwa produkcja. W różnych fazach budowy znajduje się jednocześnie około tuzina elementów struktur F-16 przeznaczonych dla konkretnych egzemplarzy seryjnych. Każdy jest dokładnie opisany i oznaczony, łącznie z klientem, do którego ma trafić dany samolot. Nie możemy tego niestety pokazać, gdyż naruszałoby to zasady bezpieczeństwa i zapisy umów z klientami.
Pokazuje to jednak, że już obecnie znajduje się w Polsce bardzo ważny i coraz większy komponent produkcji F-16 Block 70. „Zaczynamy produkcję seryjną struktur kadłuba F-16 a liczba części i wielkość zamówienia, zgodnie z zapowiedziami Lockheed Martin, będzie wzrastać. Docelowy poziom 70-80% udziału w ich budowie osiągniemy już w przyszłym roku”. - mówi prezesa PZL Mielec, Janusz Zakręcki i dodaje - „Obecnie mamy zagwarantowane zamówienia na około 50 struktur kadłubów”. Jednak zamówienia będą napływać, szczególnie w sytuacji, gdy PZL Mielec jest dziś jedynym dostawcą części z produkowanych obecnie elementów.
Na poniższym zdjęciu widać planszę z podziałem produkcji elementów struktury F-16. Elementy oznaczone kolorem jasnozielonym powstają w PZL Mielec. Ciemna zieleń, to elementy, których jedynym producentem będzie w przyszłym roku polski zakład. Oznacza to, że znajdą się one w każdym latającym na świecie F-16 Block 70/72 wyprodukowanym w Greenville.
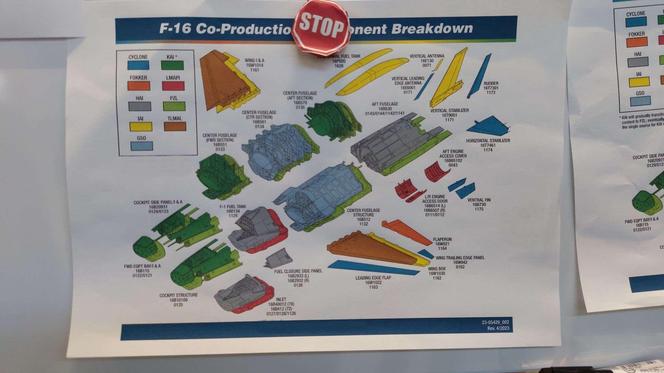
i
Rok 2024 będzie bardzo ważny dla tego programu, gdyż w Mielcu będą nie tylko produkowane seryjnie kolejne elementy, ale też rozszerzy się zakres prac na już wytwarzanych. Na przykład 3 elementy przedniej części kadłuba, które dziś wysyłane są do USA oddzielnie, będą na miejscu łączone w jeden moduł. Można pół-żartem powiedzieć, że będzie można wtedy ułożyć z gotowych części niemal kompletny kadłub F-16. Brakować będzie jedyne dziobowej owiewki osłaniającej radar, skrzydeł i stateczników, aby mieć sylwetkę myśliwca.
Od próbnych egzemplarzy do seryjnej produkcji
Docelowo PZL Mielec mają co miesiąc opuszczać cztery komplety struktur. Poszczególne segmenty nie są łączone na miejscu ze względu na wygodę transportu. Łatwiej transportować je osobno niż jako cały kadłub. Cztery sztuki miesięcznie to 48 rocznie. Może niewiele, ale jak na maszyny tej klasy, za takie pieniądze, to całkiem nieźle.
Warto też wspomnieć o tym, gdzie realizowana jest cala produkcja struktur F-16. Umieszczono ją w historycznej hali, oczywiście po odpowiednich remontach i modyfikacjach, ale w tej samej, w której powstawały samoloty szkolne PZL Iryda. Ostatnie odrzutowce, jakie produkowano w tych zakładach. Udział w produkcji F-16 to w pewnym sensie powrót Mielca do korzeni, czyli do produkcji samolotów bojowych.
Jest to również silny impuls do rozbudowy i rozwoju. 50 pracowników PZL Mielec spędziło niemal pół roku w Greenville, na linii produkcyjnej, szkoląc się do budowy struktur. , którzy stanowią wsparcie w przypadku wszelkich problemów czy wątpliwości. Obecnie na linii pracuje 72 monterów i 12 amerykańskich specjalistów. Kolejne półtorej setki pracuje przy wsparciu, magazynach i zaopatrzeniu linii produkcyjnej. Warto też odnotować, że wiele znormalizowanych elementów, takich jak śruby, nity, podkładki itp. dostarczają „do F-16” polscy producenci. W miarę jak produkcja się rozwija, zaangażowanie polskich poddostawców będzie rosło. Wbrew pozorom jest to również napływ nowych technologii i kompetencji do kraju. Już dziś PZL Mielec zatrudnia około 1500 osób, ale jednocześnie zapewnia ponad 5000 miejsc pracy w ramach krajowego łańcucha dostaw, głównie wśród firm zrzeszonych w Dolinie Lotniczej.
Budowa struktury to skomplikowana sprawa
W temacie budowy elementów F-16 w Polsce widziałem już niejedne złośliwy komentarz o tym, jak to skręca się w PZL Mielec kilka aluminiowych kawałków do amerykańskiego samolotu i mówi, że to postęp. Ale sprawa nie jest tak prosta jak się wydaje, a pod hasłem „struktura kadłuba” nie kryje się odpowiednik karoserii samochodowej.
Na przykład produkowane już seryjnie w Mielcu elementy środkowej części kadłuba umieszczone się w miejscu mocowania skrzydeł do kadłuba. To element bardzo wymagający. Nie tylko przenoszący ogromne obciążenia podczas wykonywania manewrów, gdy działające z różnych kierunków siła nośna, opór, siła odśrodkowa i pchająca maszynę do przodu moc silników starają się dosłownie wyłamać skrzydła z kadłuba. Tu również zbiegają się różne instalacje, przewody sterujące różnymi funkcjami samolotu oraz przesyłające dane do uzbrojenia.
Wszystkie te rurki, wiązki przewodów, zbiorniki paliwa i innych płynów umieszcza się w strukturach samolotu podczas ich budowy w PZL Mielec. Oznacza to skomplikowaną i precyzyjną pracę. Łączenie przewodów, rurek, elementów nośnych takich jak wręgi usztywniające konstrukcję, elementów poszycia, czyli „skóry” maszyny. Wszystkie te materiały, elementy, instalacje, trzeba połączyć w jedną działającą całość i przetestować. Również jeśli chodzi o szczelność, ponieważ wiele pozornie pustych przestrzeni w samolocie F-16 stanowi zbiorniki paliwa. Silnik odrzutowy, szczególnie w warunkach bojowych pożera je w zawrotnym tempie i każdą wolna przestrzeń warto wykorzystać na to, żeby móc pozostawać w powietrzu dodatkowe kilka minut.
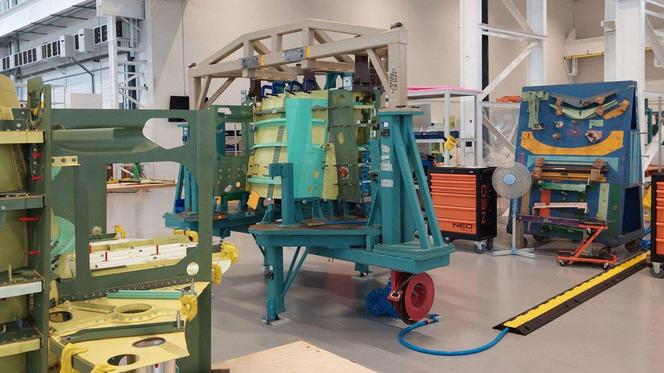
i
Dlatego każdy element, zanim opuści zakład w Mielcu, musi przejść testy, obejmujące również test szczelności. Uzyskuje się ją, stosując pomiędzy elementami specjalne uszczelniacze i dodatkowo indywidualnie uszczelnienia wszelkich połączeń. Aby uzyskać efekt, cały element struktury umieszcza się w autoklawie, czyli specjalnym piecu, w którym kontrolowana jest nie tylko temperatura, ale i ciśnienie. Jeśli element po tych zabiegach okaże się nieszczelny, nie może być po prostu „poprawiny”, ale trzeba go rozmontować, gdyż ze względów wytrzymałościowych i technologicznych nie może być ponownie podgrzany w autoklawie. To oznacza, że zarówno praca jak i jej kontrola na każdym etapie musi być bardzo dokładna.
Żeby było trudniej, różne konfiguracje części elementów są stosowane w samolotach dla różnych klientów. Mogą się one różnić wyposażeniem, więc w jednym egzemplarzu potrzebny jest jakiś określony wspornik, wiązka kabli czy dodatkowy otwór eksploatacyjny a w innym nie. Jest to oznaczone w dokumentacji każdego egzemplarza, a żeby ułatwić pracę, przyrządy służące do montowania określonych konfiguracji, czy specjalne „szablony” do wyznaczania miejsc na nity czy otwory eksploatacyjne, są oznaczone określonymi kolorami, podobnie jak miejsce na ich umieszczenie na linii produkcyjnej. Znacznie ułatwia to pracę i zmniejsza ryzyko błędów.
Mimo wszystko jest to skomplikowana i wymagająca praca, a każdy błąd może kosztować firmę tysiące, jeśli nie dziesiątki tysięcy dolarów. Praca nie przypomina tutaj taśmy produkcyjnej w fabryce samochodów, ale raczej ręczne wytwarzanie jakiegoś ekskluzywnego modelu na indywidualne zamówienie.
To praca wymagająca wysokiej klasy specjalistów i nic w tym dziwnego, że trafiła do Polski. Jeśli czegoś w naszym kraju nie brakuje, to dobrze wykształconych, wysoko kwalifikowanych specjalistów w zawodach technicznych. Koncentracja przemysłu lotniczego w rejonie Mielca i szerzej tak zwanej Doliny Lotniczej z pewnością ułatwia optymalizację w tym zakresie, a płace też nie należą do najgorszych. Mimo to, z pewnością w Polsce koszty są niższe niż w USA, nawet jeśli doliczy się koszty transportu. Obie strony są więc zadowolone, czerpią zyski i osiągają nowe możliwości. Nic więc dziwnego, że PZL Mielec jest dziś największym zakładem produkcyjnym amerykańskiego przemysłu lotniczego i wojskowego, który znajduje się poza terytorium USA. A jego możliwości nie sa jeszcze w płeni wykorzystywane.